How Is the Heart of String Transport Created? A Report on the Work of the Electric Drive Bureau
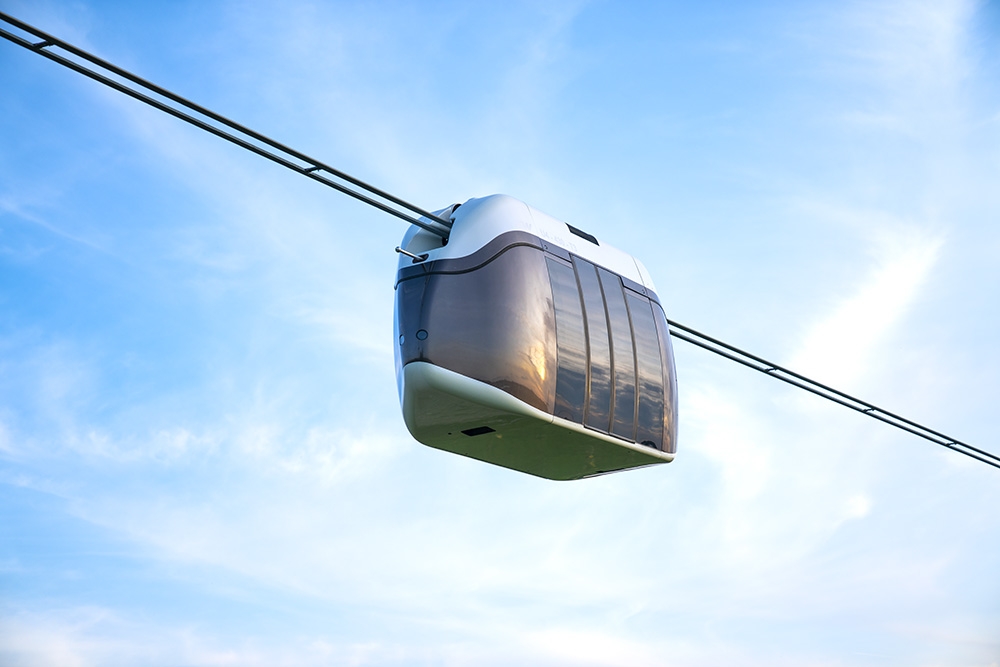
With this publication, we begin a series of reports on the design bureaus of Unitsky String Technologies Inc. Today we will talk about the Electric Drive bureau. It is here that the heart of string transport is created — electric motors, as well as other important components of uPods. Details are in the report.
Ilya Zhagalsky, Head of the design bureau, explains how important elements of string transport are designed and assembled:
— Our bureau was set up at the end of 2017. There were only 7 people in it at that time. Today we have 17 engineers and 7 people working at the assembly sections — a total of 24 professionals.
Our design bureau is engaged in the development and manufacture of electric motors, energy storage devices, power converter equipment, electronic units. In addition, we are developing circuit engineering and topology of printed circuit boards of electronic devices, the required software for both microcontrollers and personal computers.
The design bureau also develops and manufactures the equipment necessary for assembly and testing. For example, specialists of the Electric Drive design bureau have developed and manufactured a load bench for testing energy storage devices. Its peculiarity lies in the fact that the required load can be set for the energy storage devices by simply clicking on the touch-sensitive control screen.
During the designing development, the engineers of the department carry out realistic simulation of thermal and electromagnetic processes.
In fact, the design bureau has implemented a full cycle from the development of technical specification “at the input” to the production of a finished product “at the output".
Our Electric Drive design bureau is located at the production facilities of the factory “SW Plant”. This allows to speed up the process of creating motors, converters, energy storage devices, electronic units. Due to the location of the bureau at the production site, the designers promptly solve the issues arising in the manufacturing process and make the necessary changes to the project design documentation.The employees of the assembly sections, being in constant interaction, receive the necessary advice from the developer.
What are the tasks of designers?
Viktor Kudrin is engaged in the layout and packaging of converter equipment and electronic units. The bureau employee proudly tells:
— Our products are at the level of foreign analogues in their features, and in some parameters, they surpass them.
Andrey Khvalyov, lead design engineer, is engaged in the development of electric motors:
— We create electric motors for each vehicle, taking into account the necessary requirements: rotation speed, torque, maximum efficiency zone.
All energy storage devices for string transport are designed and assembled by the Electric Drive design bureau. Lead design engineer Yuri Shrubok says that at the moment the team is working on an energy storage device for the 5th generation transport, which can be replaced in transport without human participation. The priority during development is safety, cost-effectiveness and durability of the storage device.
— Assessing the current global trends and basing on our own rich experience, we create unique energy storage devices for our vehicles. Currently, a quick-detachable energy storage device is being developed. It has optimal dimensions and capacity. It is more resistant to external impacts, more technologically advanced and durable, and most importantly – safe, says Yuri Shrubok.
Ilya Zhagalsky explains that the energy storage management system (developed by the Electric Drive Design Bureau) monitors the voltage on each battery cell in real time (their number in the storage reaches 400 pieces), the temperature inside each unit and other operating parameters. All batteries are equipped with active or passive balancing, as well as a cooling and heating system. This allows the batteries not to overheat at high temperatures and keep warmth at low temperatures. The safety of the storage devices is in the first place.
How does the assembly proceed?
Components are manufactured according to the design documentation worked out by the design bureau. Then they are delivered to the assembly sections. At an assembly section, where electric motors are assembled, we get acquainted with Alexander Kovalik.
— All parts for the electric motor are of our own design and manufacture. For 6 years of work, a line of 8 types of electric motors for our transport has been created, Alexander proudly says.
The specialist emphasizes: the closest attention is paid to the quality of the products.
At the next assembly section, an employee of the design bureau Oleg Dmitry has been collecting energy storage devices for string transport for 4 years now.
— All storage devices are unique, have a different design, capacity and power. We manufacture them for each specific vehicle model.
Oleg says that a lot depends on the assembly, and most importantly — the reliability and safety of the product.
What happens after the assembly?
After assembly, the products are passed to the laboratory, where the technical features embedded in them are checked.
Electrical engineer Alexander Andrianov checks the products for compliance with their technical specifications.
— We work with modern professional equipment that allows us to analyze the parameters of a running electric motor. Based on the information received, a decision is made on the need to adjust its parameters or to install it on a vehicle.
According to Ilya Zhagalsky, the enterprise has a good material and technical base, which makes it possible to significantly simplify and speed up the process of developing and manufacturing products.
More news
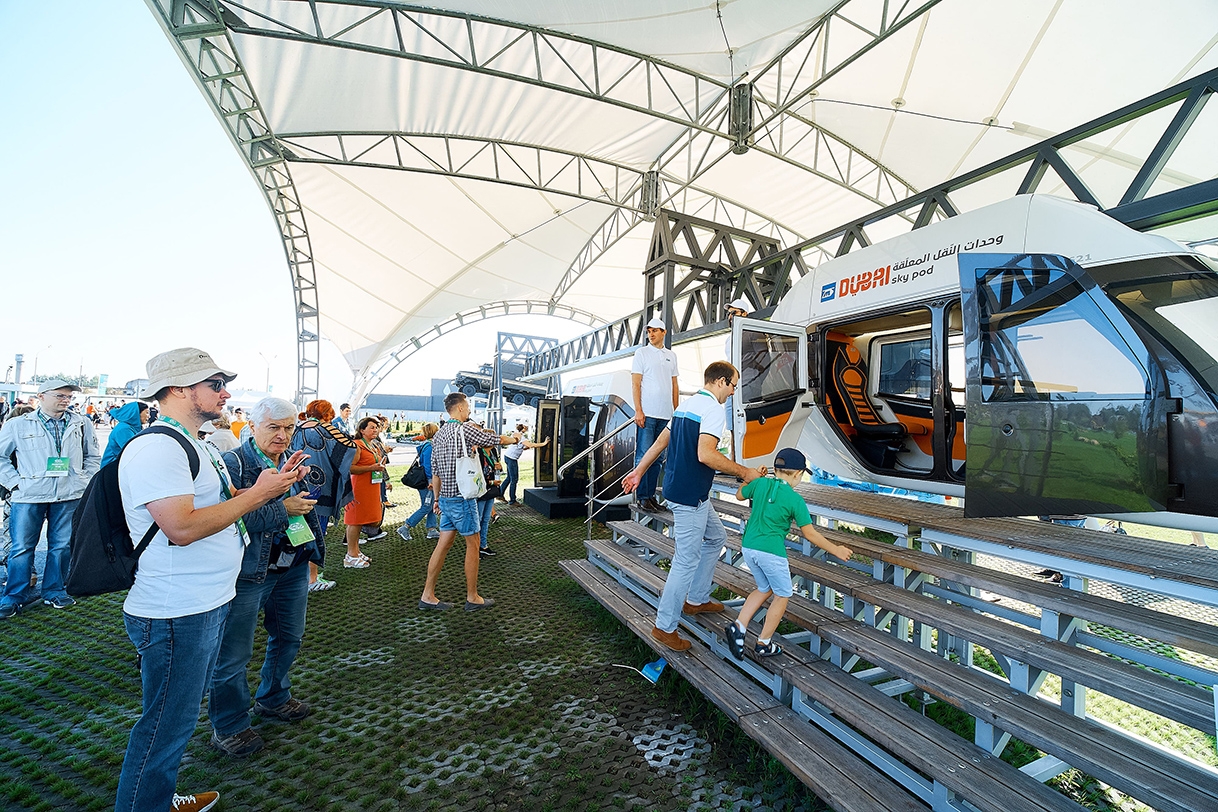
Blog
29 August 2023
uST Technology to Help Deal with Pendulum Migration
uST Solutions can be adapted to the problems of large cities and, in particular, to the optimization of transport communication based on the scale of pendulum migration. Even with the existing development it is possible to set up convenient routes along an optimal path and avoid large-scale road works.
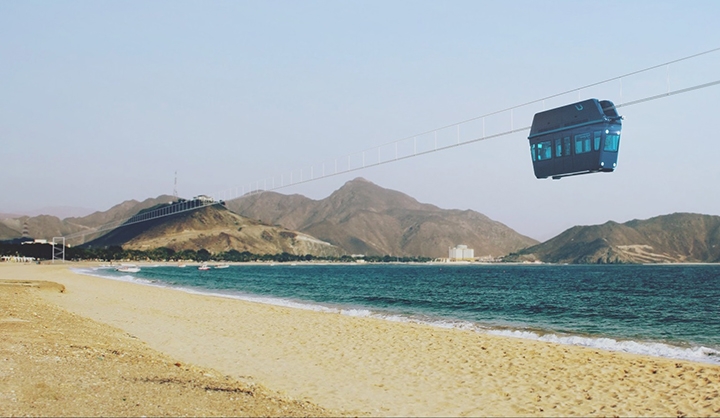
News
12 April 2023
A New uPod by UST Inc. Was Delivered to the uSky Center
uBus U4-212-01, the company’s newest development, has arrived at the uSky Test and Certification Center. Here will be held experimental and industrial tests on the suspension track with a length of more than 2 km that is currently under construction.
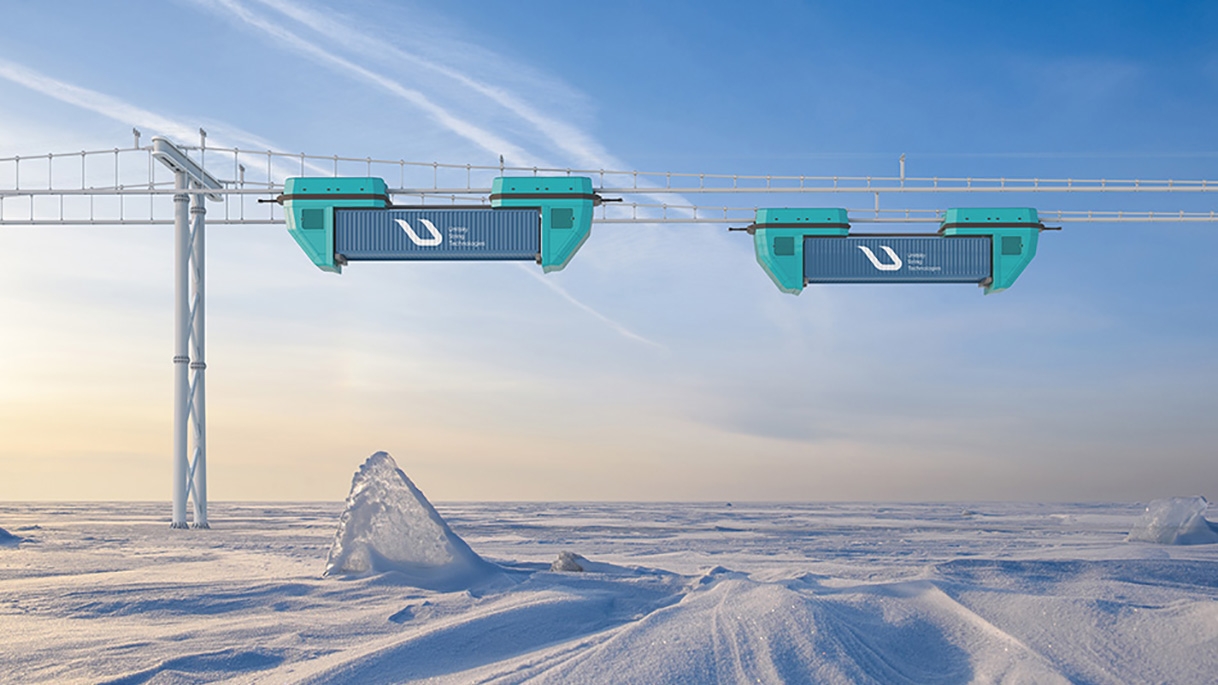
Blog
5 January 2024
Why Transportation in the Far North will be Cheaper with uST Technology
uST Transport & Infrastructure Complex, a unique cargo and passenger transportation technology, is easily adaptable to any region.