Can the string rail be restored?
The lifespan of the string rail overpass of the uST transportation and infrastructure complex is 50 years. It is maintenance-free and very reliable structure. However, what if the overpass requires repair? For this situation, the experts at UST Inc. have devised a streamlined and efficient method for the restoring of prestressed steel structures subjected to continuous dynamic forces. This technique is particularly useful for the restoration of the string rail raceways and bodies.
Why is this significant?
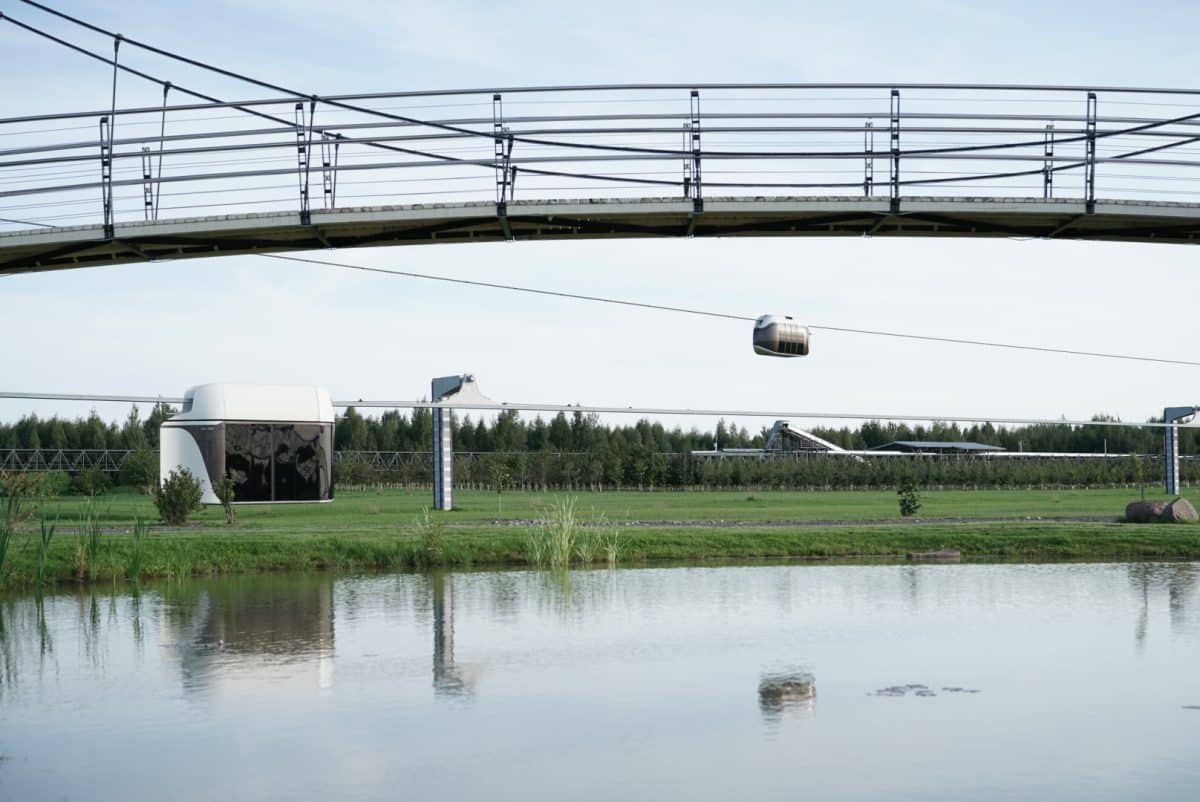
In the process of installation and maintenance of the transportation systems, it is not uncommon for track components to sustain damage. For example, if a rail unmanned vehicle slips during testing in different modes, scratches may appear on the surface of the rail, which could negatively affect traffic safety.
Problems of common methods
During the regular maintenance of railway tracks, any defects are repaired by grinding or replacing the damaged sections. However, these methods are not suitable for string rails. The raceway is made of a particularly strong alloy steel with a small thickness, and deep grinding could reduce the strength of the structure. Replacing an element involves complex calculations and requires de-stressing the section, which can be time-consuming and expensive.
A new approach to repairing
If it is not possible to replace or repair the damaged area, the engineers have proposed welding metal onto it. This method seems simple at first, but it requires careful selection of the right electrode and strict adherence to welding techniques in order to achieve a strong metal joint. If this is not taken care of, the deposited layer may become detached.
Restoring stages
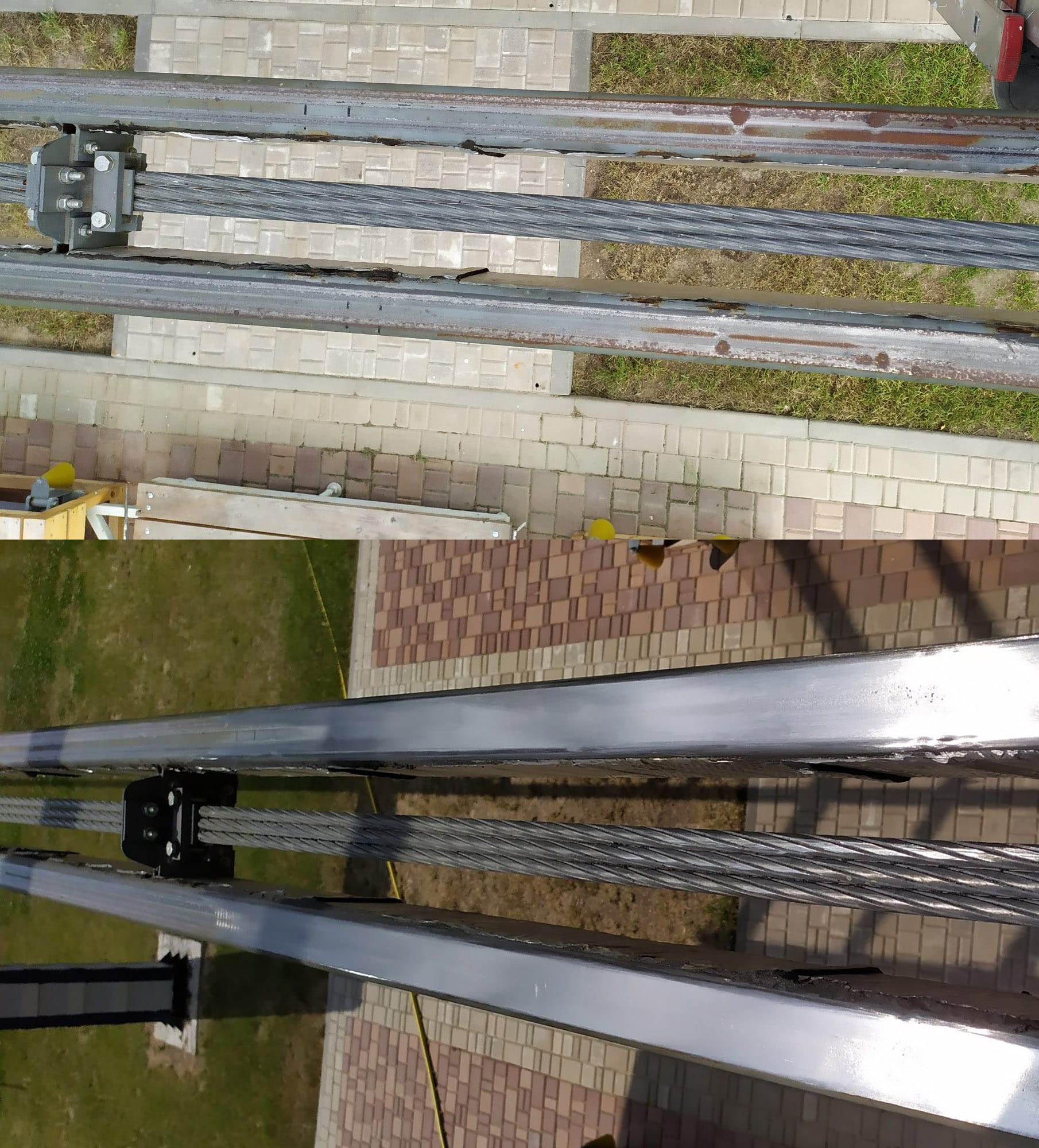
Before starting work, it is necessary to mechanically remove the zinc coating from the defect site, and then heat the surface using a gas burner or hot air gun to 80–100°С. The electrodes are being heated at a temperature of 320-350°C for two hours, after which they are stored in a heated quiver.
Arc surfacing is done in layers until the design thickness is achieved. It is important to ensure that the temperature between the layers does not exceed 150°С, and after the work is complete, the deposited metal should cool down to 40-50°С. Subsequently, the surface is inspected for any cracks or imperfections, and then it is grinded, cleaned, and treated with a zinc-rich compound.
Durability and simplicity
The technology proposed by Belarusian engineers allows for quick and reliable rail repair without the need for highly specialized technicians. All that is required is knowledge of steel specifications and a skilled welder. In EcoTechnoPark (Maryina Gorka), these sections have been operating without any complaints for more than five years. The repair site is not visible to the naked eye and requires specialized knowledge to locate.
More news
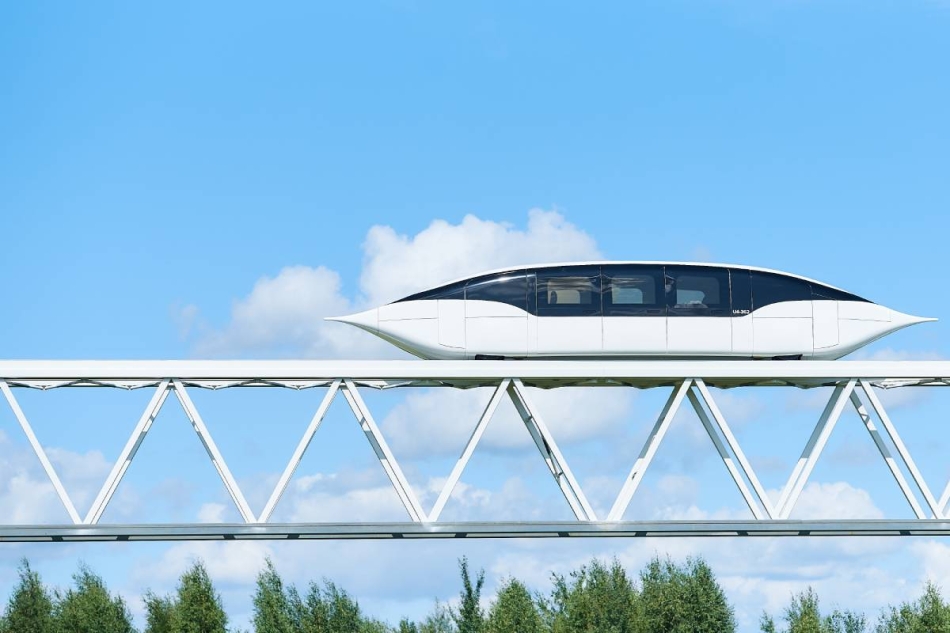
News
27 February 2025
Development of High-Speed uST Direction Will Reach New Heights
The development of high-speed transport will enter a new phase, bringing its practical realization closer.
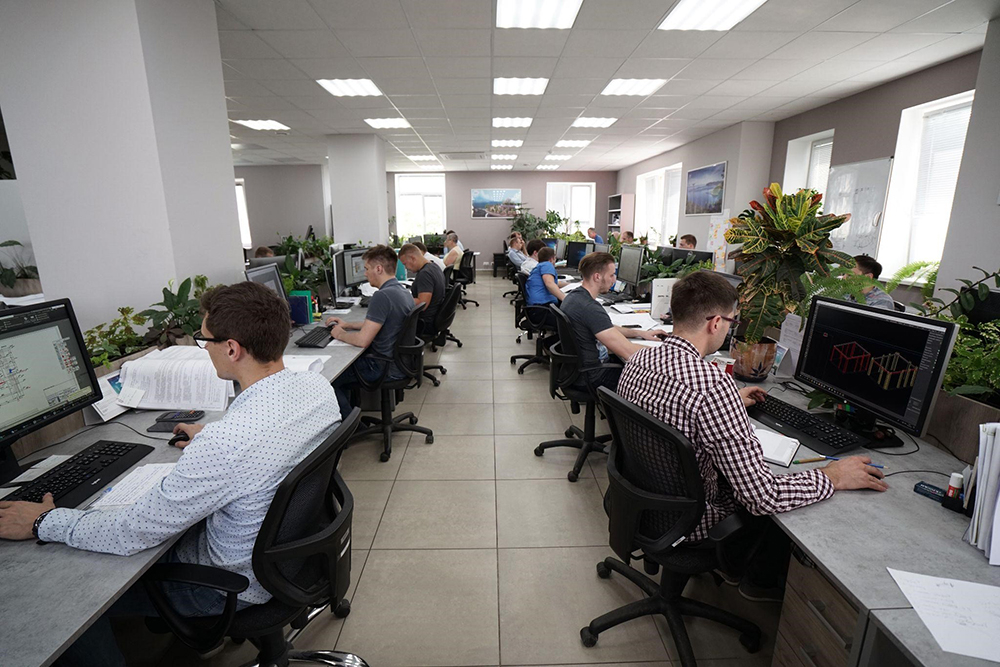
News
27 May 2022
Unitsky String Technologies Inc. Successfully Passed the Audit
UST Inc. passed the annual audit of individual financial statements, which was conducted by FinExpertiza-Bel Audit LLC. Annual individual financial statements accurately reflect the financial position of the company.
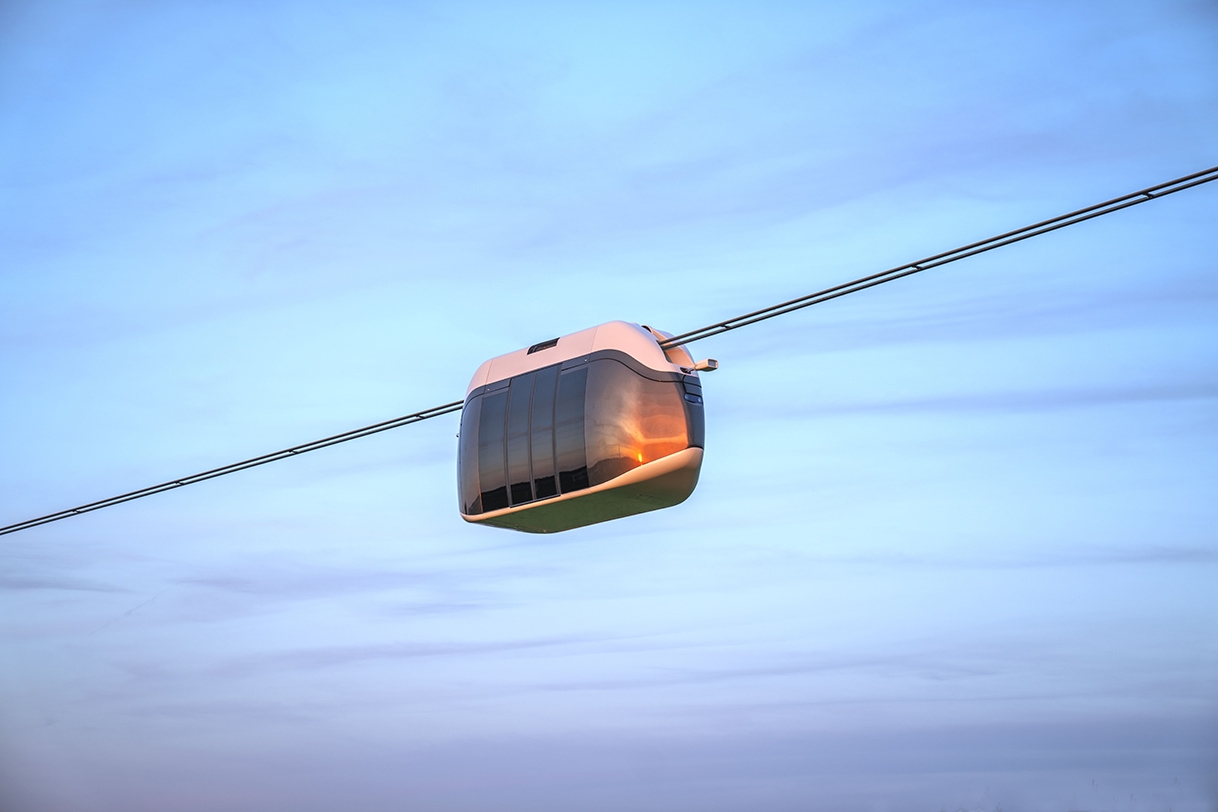
Blog
4 September 2023
How can uST transport help to cope with driver shortages?
The global shortage of human resources has serious implications for the logistics industry.