A 50-Year Service Life and Beyond: What Solutions Did UST Inc. Engineers Lay Down When Designing the uLite Route?
The creation of the uLite multipurpose complex included several areas at once. One of them is the design of the track structure. How did this process unfold and what solutions did UST Inc. specialists lay down when developing the track?
From ideation to implementation
Alexey Savitsky, Lead Design Engineer at the Transport Overpass Design Office, says that the company's engineers were primarily focused on the weight parameters of the uPod:
"On this basis, we calculated the load on the rail, and then thought about the track structure. The uLite is a fairly lightweight uPod, and the track structure should also be lightweight, with a simple and functional design. We considered many solutions to find the optimal one and settled on the flexible rail as the most suitable track option by all criteria."
The track structure of the uLite complex has a number of features. Firstly, the track is marked by a high-tech installation and can be built in a short period of time even in areas with difficult terrain. Secondly, it is the first time that aluminum rail body is used in the track structure design. Aluminum has a lower weight compared to steel, ensuring the lightness of the track. In turn, the high surface quality available in the manufacture of aluminum elements made it possible to reduce the noise impact at the wheel—rail interface.
"The unique shape of the rail body, developed by UST Inc. experts, was manufactured according to our drawings by a Russian company using the aluminum extrusion method. This is a process in which the material is heated until it becomes soft and then pressed through a molding hole. This method allows you to get an element of almost any desired shape. It would be too labor-intensive and expensive to make such a case in steel," commented Alexey Savitsky.
The basis is groundless installation technology
The track was erected using a groundless installation method. This means that not a single element of the track structure touched the ground. At the first stage, the company's specialists installed the track elements – anchoring nodes and saddles. Then the ropes (two for each rail) were stretched along the entire length and tensioned. The next step was the installation of aluminum rail bodies and their compression, after which the bodies were fastened to the ropes.
"When designing the cross-section of the track structure rail with aluminum body, we also considered its thermal expansion. Materials have a property to shrink in the cold and expand in the heat. The point is that aluminum bodies were delivered not as a single piece for the entire length of the track structure, as, for example, ropes, but in separate parts. If you install them butt to butt in summer, they will shrink in winter and the length will decrease. This will lead to gaps between the bodies, i.e. the integrity of the rail will be compromised. To avoid this, we initially compressed the body using jacks and specialized equipment," said Alexey Savitsky.
A 50-year service life
Among the main advantages of the uLite track structure are resistance to external impacts and durability. The track is designed for the temperature range from –40 to +60 °C. It does not require regular replacement of its elements. The service life before overhauling is 50 years.
Alexey Savitsky noted that the company's specialists tried to protect all elements of the track structure from corrosion as much as possible:
"For example, we looked for the most advanced zinc coating technologies. Bolt joints and elements in the anchoring node were treated with special preservative compositions to prevent moisture ingress."
When developing the track, UST Inc. engineers also took into account the peculiarities of the terrain and the tourist orientation of the facility. The flexible track structure turned out to be the most optimal solution because of its visual lightness and aesthetic design that complements the uniqueness of the Aquarelle complex without disturbing its harmony.
More news
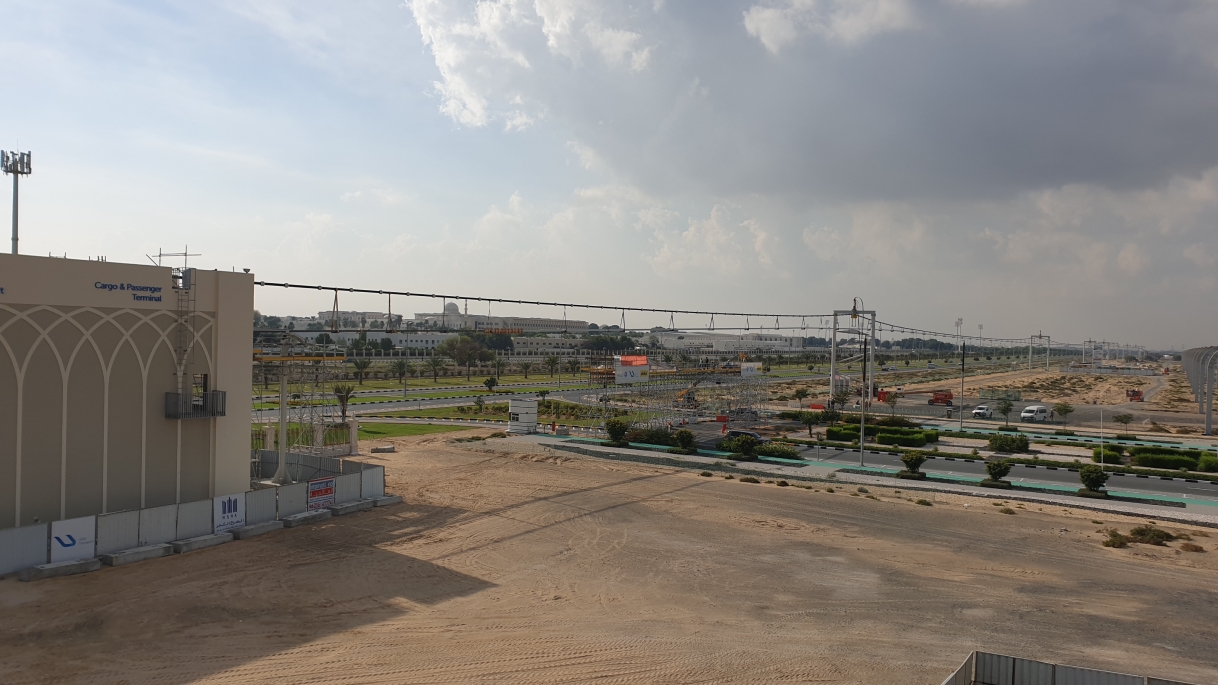
News
23 January 2023
Unique World Experience: The Elevation Phase of the Track Structure at the uSky Test & Certification Centre Was Completed
The unique elevation of a long uncut structure was completed in Sharjah, the uSky Test & Certification Centre. Similar work has not been performed anywhere else in the world until now.
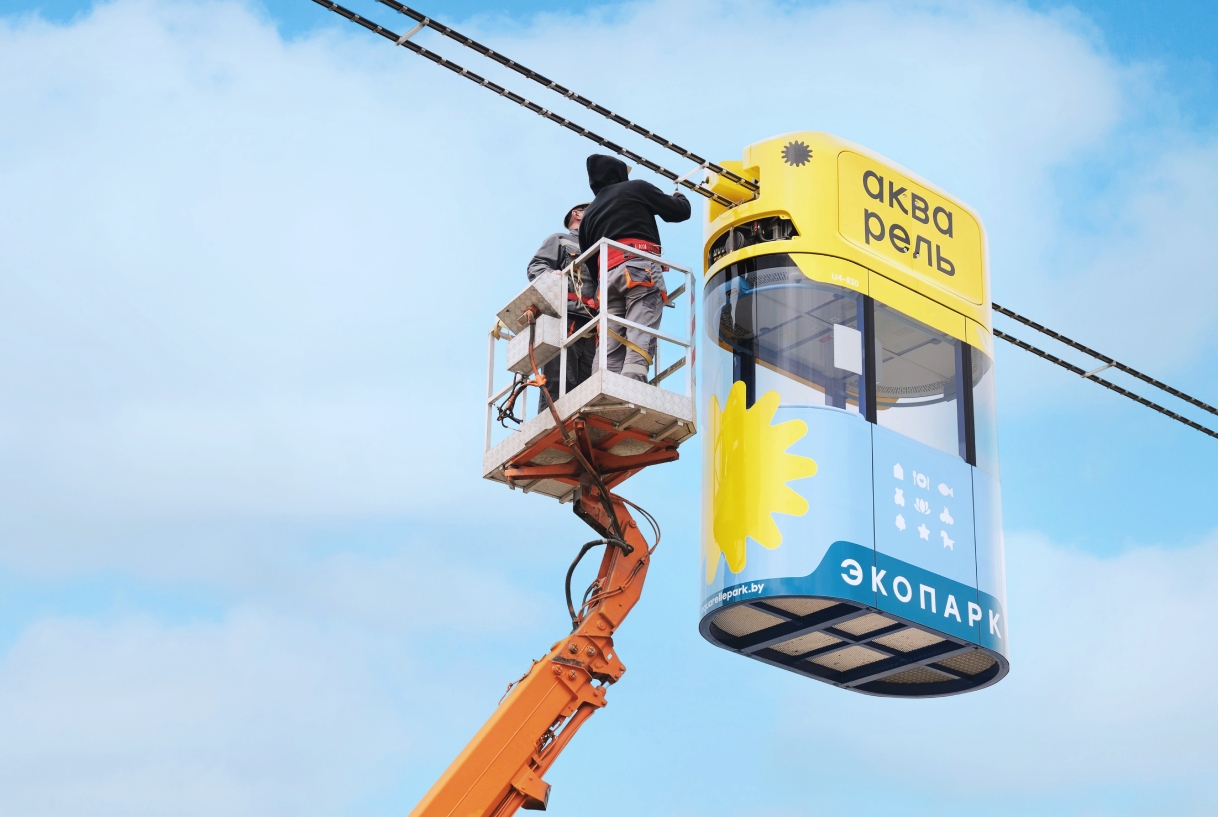
uLite
23 February 2024
Minimum 25 Years: Why Is uLite’s Design So Durable?
On the example of uLite we will demonstrate how thoroughly the company approaches the choice of engineering solutions when creating uST transport.
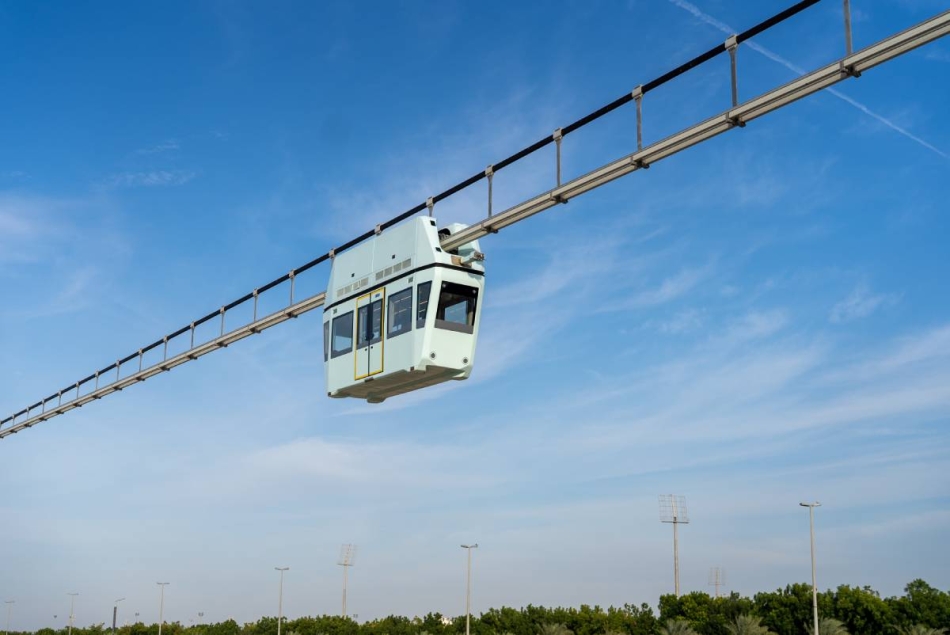
News
24 December 2024
uSky Conducts Unique Tests to Assess the Comfort of the Karat uBus
The uSky Test & Certification Center hosted unique tests of the 25-seat uBus "Karat". Engineers analyzed how comfortable passengers felt while travelling in the uBus.