The debugging of the uBus Karat control system has started in the uSky Center
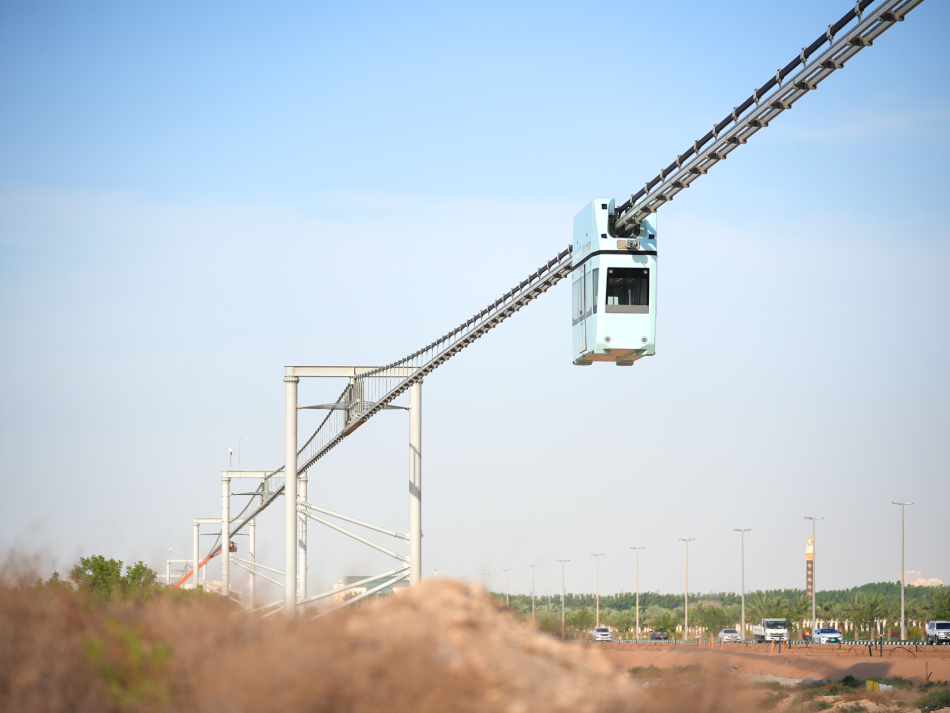
The fourth stage of dynamic testing of the transport overpass with a semi-rigid track structure and uBus Karat U4-212 goes according to schedule. Now engineers at the uSky Test and Certification Center set up the control system operability along with connecting the complex to the control room.
The automated control system (ACS) is responsible for the trouble-free and safe operation of the uST complex. It includes an external and onboard systems. The uBus movement is monitored using radio tags and GPS sensors, as well as other means of speed control and positioning. They are installed along the entire route, at stations, and in the vehicle itself. At the same time, the situation on the track is monitored by the dispatcher. Using specialized software, he observes the uBus and independently coordinates its movement.
The automated control system minimizes the influence of the human factor, thereby ensuring the safety of the entire transport and infrastructure complex. Based on the information collected in real time from its components, it allows you to make effective decisions:
- Assess threats and obstacles in the way of uBus movement using a sensor system;
- Automatically inform the central control system of any failure and emergency situation that occurred onboard the uPod;
- Duplicate the uBus communication system with the central control system (via two different channels);
- Manage all nodes and transport systems from the control room.
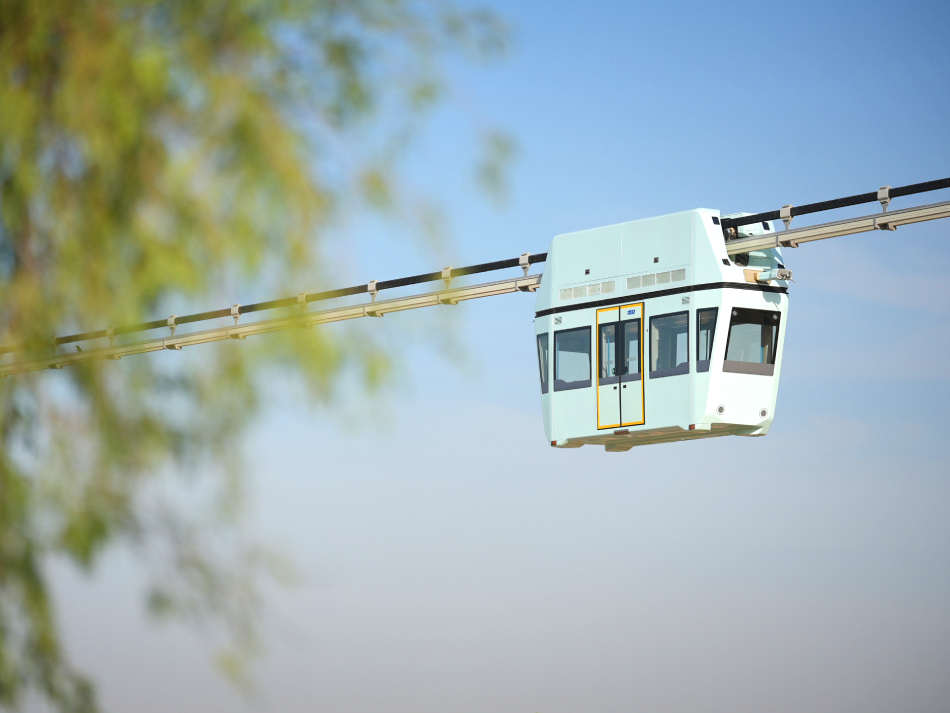
“In terms of the onboard control system, we have implemented new solutions for self-diagnosis of individual subsystems. This should potentially reduce the time required for troubleshooting. For example, in order to track whether there is enough freon in the microclimate system, now there is no need to wait for a critical decrease in pressure. The built-in self-diagnosis function is responsible for monitoring this indicator. It takes into account environmental conditions and compares them with the readings of pressure and temperature sensors,” said Evgeny Kuratovich, a Lead Design Engineer of the Software Development Division.
In the graphical part of the engineering interface (an application that shows serviceability or malfunctions in the uPod), the management capabilities of nodes of various transport systems have been expanded. So, after replacing the components of the cooling system (circulation pump, for example) a service engineer can check their operability. Also, this functionality allows you to quickly locate the fault location.
In addition, the company’s specialists have developed the intuitive interface which allows you to manage transport systems in automatic mode and monitor their condition. At this stage, separate units, which are responsible for detailed visualization of the operation of the different systems such as power supply, hydraulic, pneumatic, electric drive, cooling, and microclimate ones, have been debugged.
Let’s recall that after the commissioning is over, the transport will undergo testing of various systems and will be checked for safety and comfort.
More news
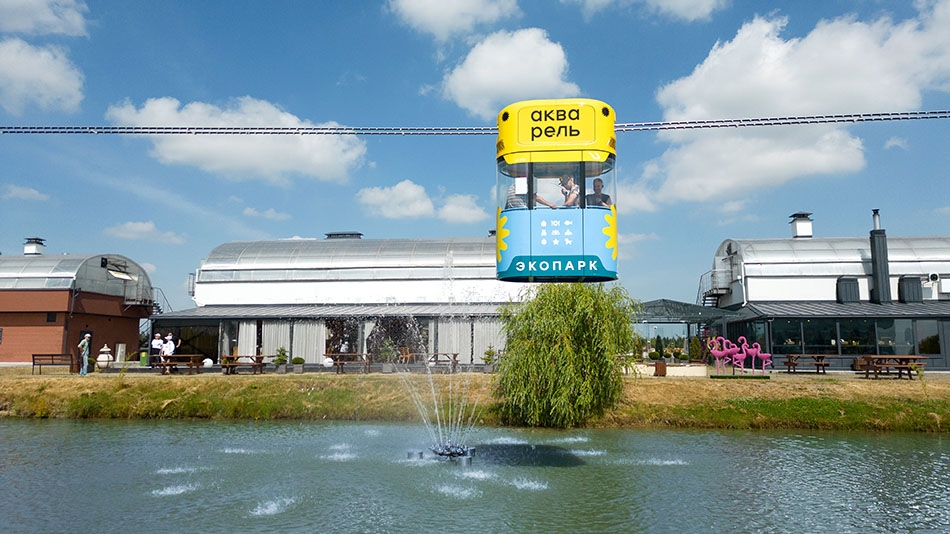
Blog
10 May 2024
Even a flood would not stop the uST complex operation
The uST transport and infrastructure complex can prevent supply collapse and isolation in flooded regions.
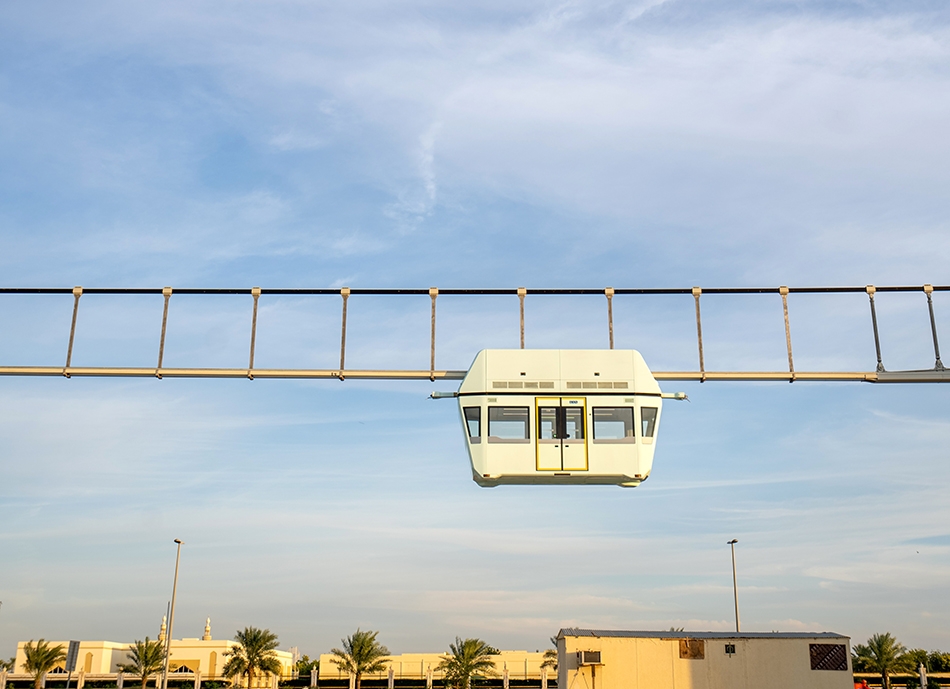
News
15 February 2024
Karat: what makes the UST Inc.’s complex stand out?
The fifth generation uPod uses improved uST engineering solutions and Karat is at a fundamentally new technological level.
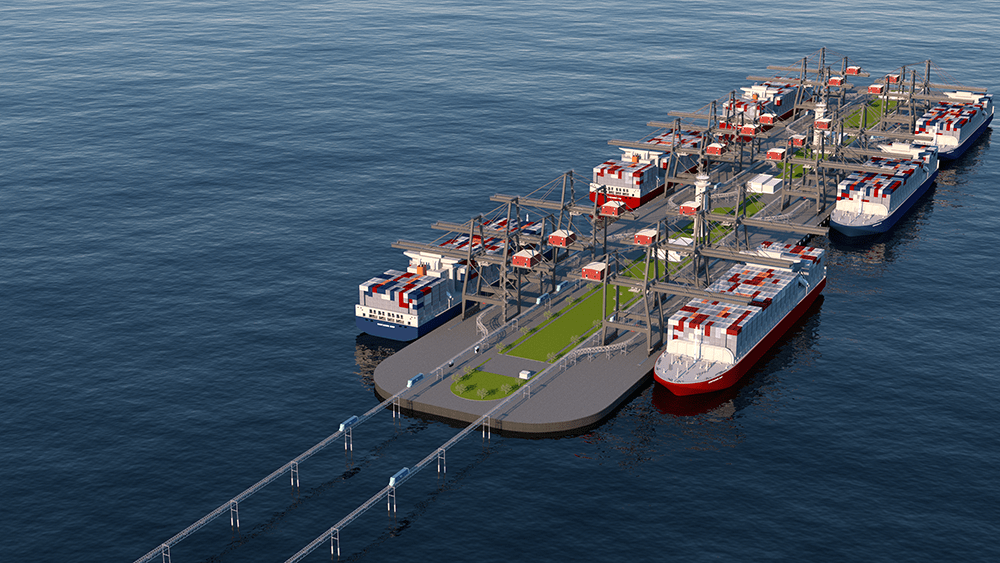
Opinion
8 August 2022
PortNews: “How Can String Technologies Reduce Port Construction Costs?”
The leading Russian information and analytical agency in the field of maritime and river transport has published a special project on the possibilities of using string technologies in the field of maritime cargo shipping.