Reduces the cost of quarrying: how the uTrans complex works
Quarrying is always associated with high financial costs. uTrans, the aboveground automated transport and infrastructure complex by UST Inc., can reduce them. Designed specifically for efficient delivery of bulk cargo, it replaces the work of a dozen dump trucks. See our article for more information about this complex.
Why using dump trucks is costly
What does typical quarry operation look like? An endless stream of dump trucks loaded with rock rises up the serpentine and goes down for a new batch. All this operates as a single system, according to a rigorous schedule. To achieve this result, the work of hundreds of skilled professionals is required.
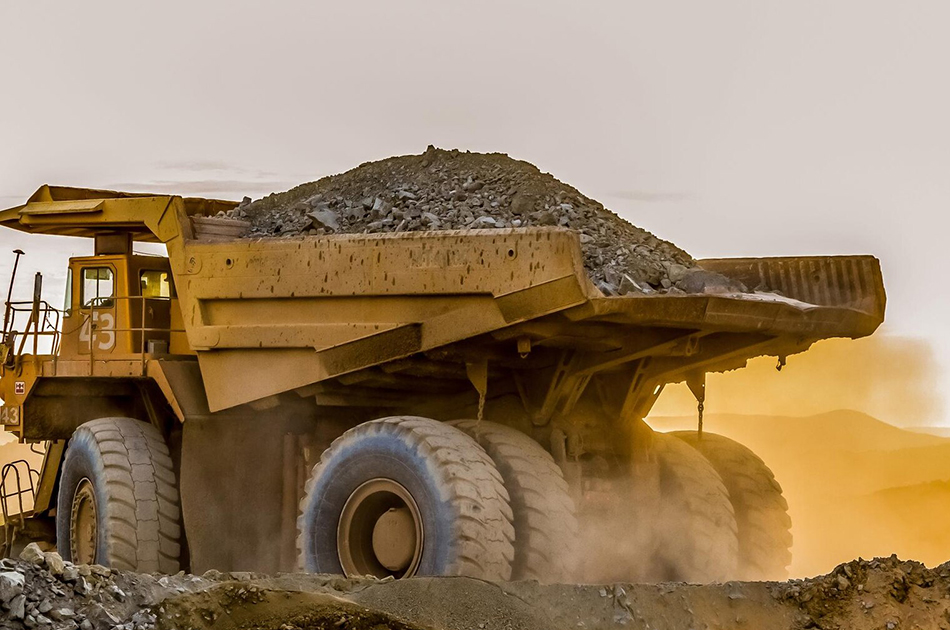
But this is not the only thing that impacts the smooth operation of the quarry. Weather conditions are also important. During the off-season – in autumn and spring – precipitation can destroy the roadway, which needs to be constantly repaired because every pothole or pit puts a significant load on the suspensions of dump trucks. The mechanisms wear in such operations is high, as is the fuel consumption. The total cost of transporting the rock is more than half the total expenses of the quarry owner.
The uTrans complex developed by UST Inc. helps significantly reduce the cost of running a quarry, eliminating spending on fuel, spare parts, equipment, salaries for drivers and much more.
How the uTrans complex is designed
The uTrans complex, designed for the needs of the mining industry, is modular in design. This allows it to be quickly adapted to any landscape. The complex consists of five main components:
- Loading terminal;
- End anchoring structure;
- Supporting tower;
- Intermediate anchoring structure;
- Unloading terminal.
All processes in the complex are under double supervision. The automated control system handles most of the work. In turn, its operations are monitored by a small team of dispatchers working in shifts.
The control room itself can be structurally integrated with an anchoring structure, whose design provides enough free space that can also be used for the placement of a service center.
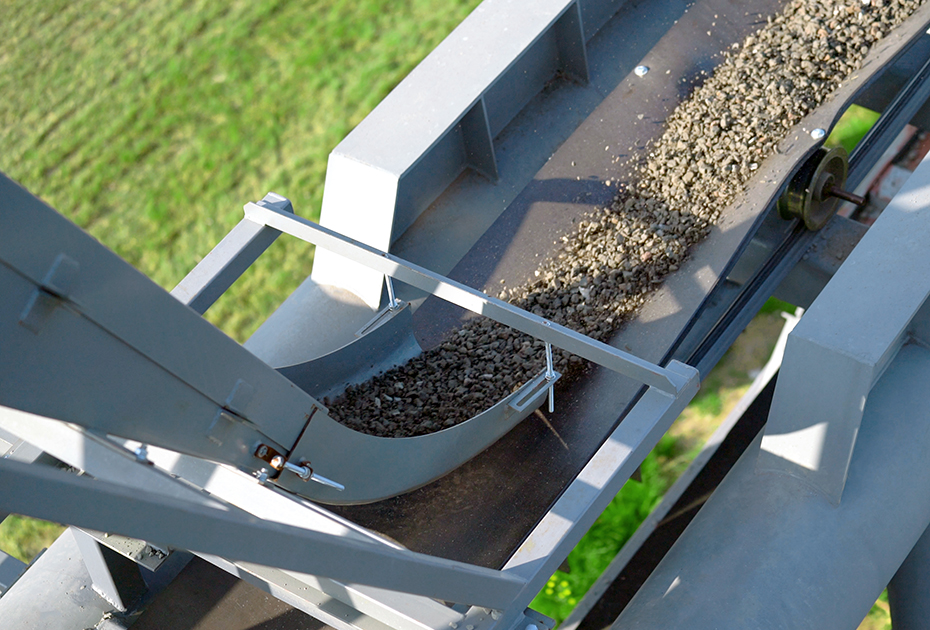
This is very convenient as it allows for technical inspection and maintenance of the complex, as well as scheduled and ongoing repairs right on the site.
The complex requires only 35 people to operate: eight dispatchers and 27 specialists in the maintenance of technological sites along with a service center. Their training will take about six months.
How the rock is transported
A multi-wheeled continuous mechanism is used for the transportation of bulk goods. It is, in fact, a ring-shaped transport belt located on a semi-flexible string rail overpass.
This design prevents local deformations of the belt and requires less degree of its tension. This results in a 2-3x increase of the belt life. The rock transportation speed reaches 10 meters per second. Its loading and unloading are carried out without the involvement of maintenance personnel. The complex is able to operate around the clock, regardless of weather conditions.
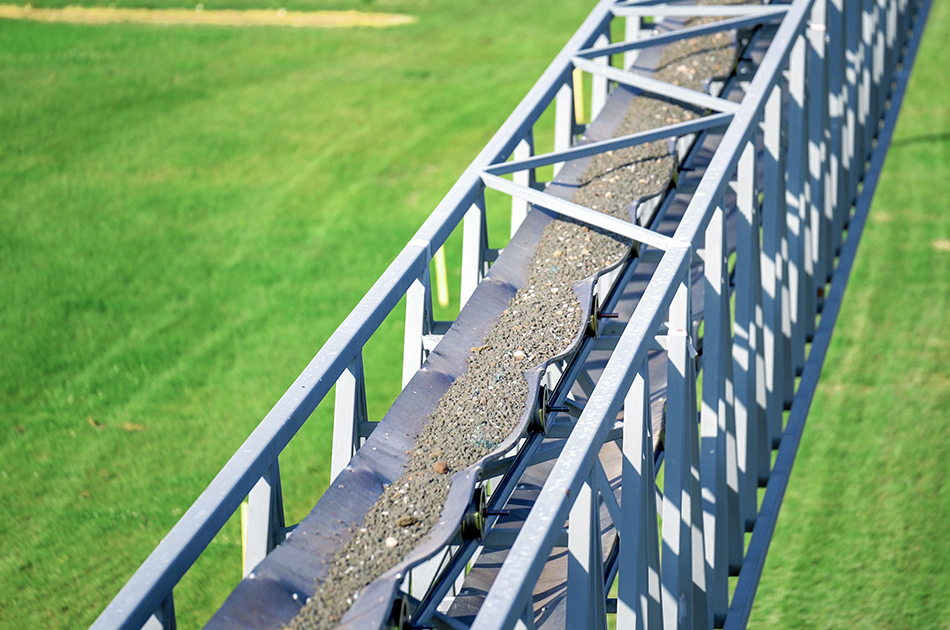
The length of the belt has no restrictions. The distance between the supports of the string rail overpass reaches 1500 meters in a special design, which means you can transport rock over any terrain and through almost any obstacles. The incline to be overcome reaches 55%. The uTrans complex is capable of transporting up to 100 million tons of rock per year.
What is the advantage of the uTrans complex?
To demonstrate all the advantages of using uST technology, we will give a clear example. Let’s calculate the cost of transporting the rock over a distance of 10 kilometers with a quarry capacity of up to 15 million tons per year.
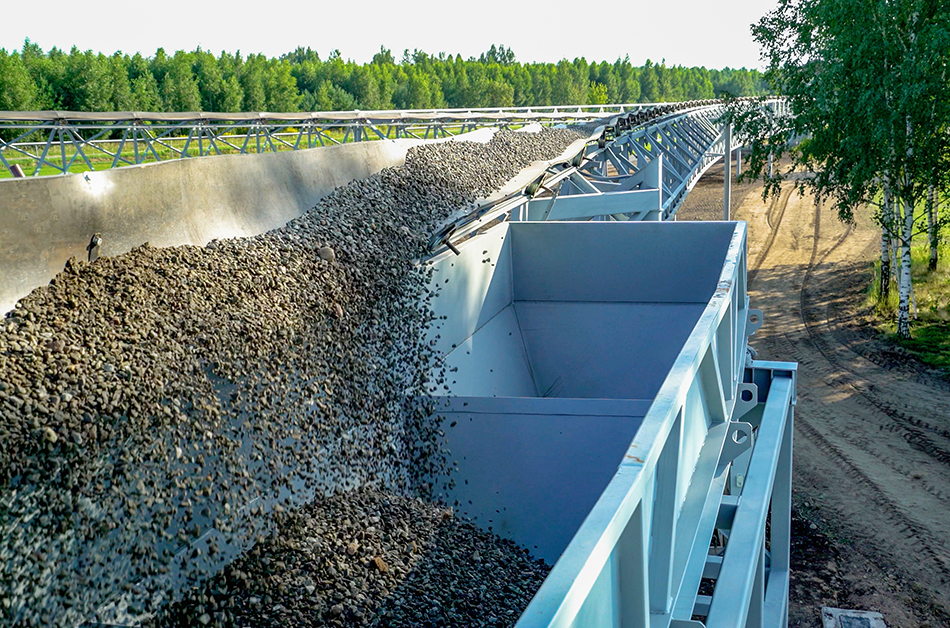
Let’s say our fleet consists of 50 four-axle dump trucks with a payload capacity of 25 tons each. 150 drivers will be required to operate them. When working in three shifts, they will be able to make 1,600 rides per day and spend 8,160 liters of fuel during this time. About 3,000,000 liters of fuel will be used per year with a total cost of 175 million Russian rubles. About 170 million Russian rubles will be spent on employee remuneration over the year.
uTrans will require 35 employees in such conditions. The complex will use 10,125 kilowatt-hours per day and 695,625 kWh per year respectively, which will cost about 25 million Russian rubles. The salary costs for the employees will amount to 15 million rubles.
The fuel costs when using the complex will be seven times less, while the salary costs will be 10 times less.
How long does it take to build the complex?
The commissioning of uTrans takes from 1,5 years, depending on natural and climatic conditions, design characteristics and the number of objects in the complex.
uTrans is characterized by low metal consumption, does not harm the environment and requires minimal land acquisition. Its route can pass through protected areas without disturbing local flora and fauna.
Choosing uTrans would reduce the cost of operating a quarry by over half, allow for a significantly smaller number of personnel, and minimize environmental harm.
More news
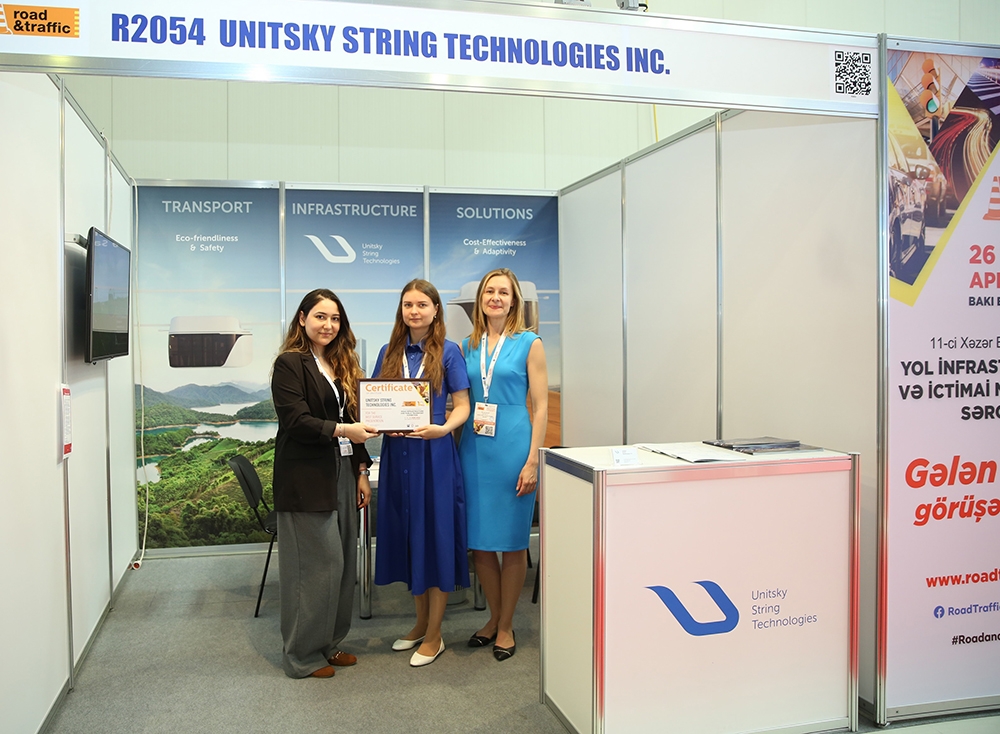
News
7 Junе 2022
Railway Technology: UST Inc. Took Part in the International Exhibition in Baku
The British media Railway Technology has posted a publication on its website, which tells about the participation of Unitsky String Technologies Inc. in the 10th Anniversary Caspian International Road Infrastructure and Public Transport Exhibition. The event was held from June 1 to 3 in the capital of Azerbaijan.
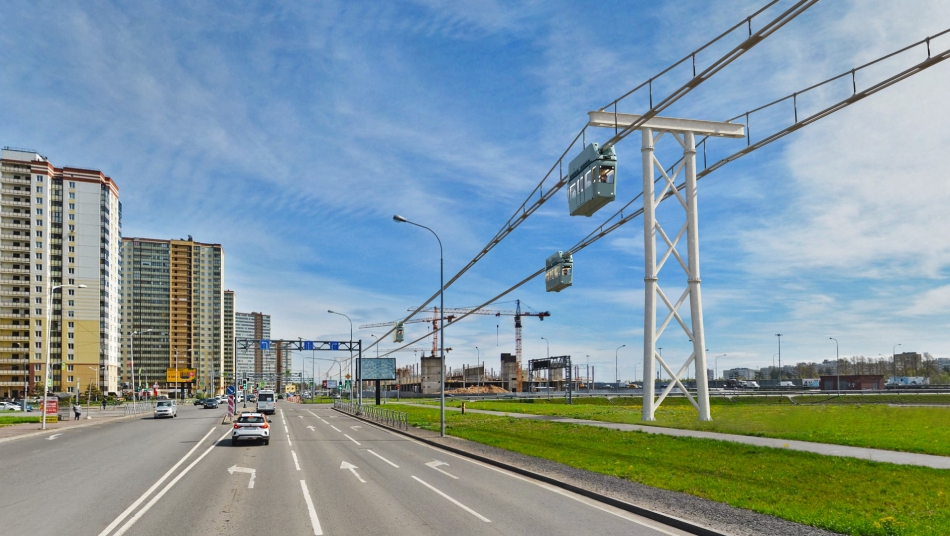
News
28 January 2025
Experts from Various Fields Will Share Their Views on the Prospects of uST in Russia
Soon, a comprehensive overview article will be published on the UST Inc.’s website. In this article, we will discuss in detail the potential for introducing string rail transportation in Russia.
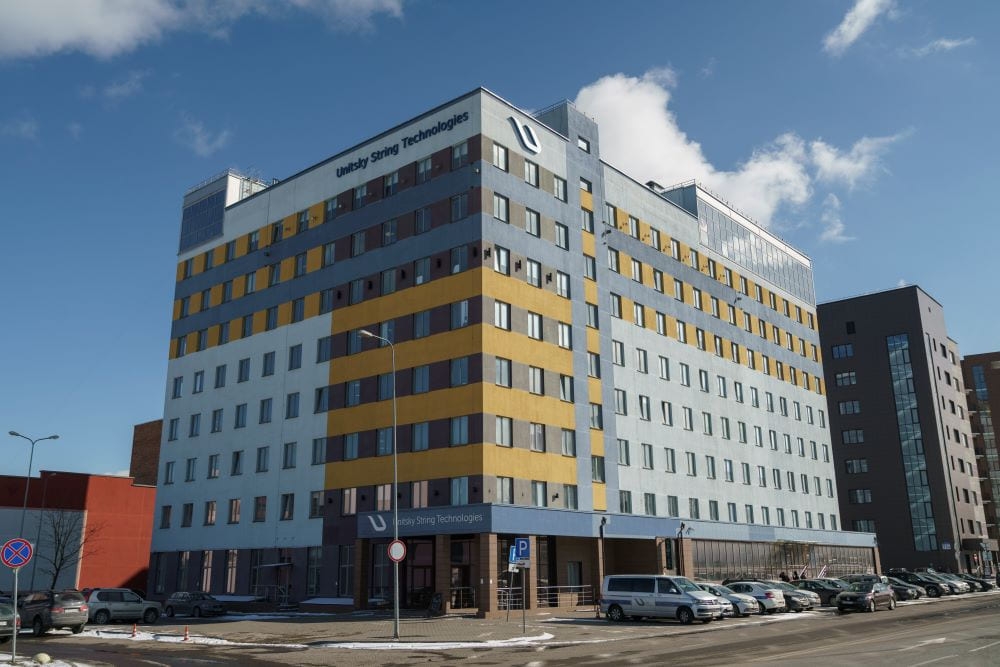
News
15 July 2022
Unitsky String Technologies Inc. Has Successfully Passed Another Audit
BDO LLC conducted an audit of the financial statements of Unitsky String Technologies Inc. in accordance with International Financial Reporting Standards.