UST 2021: Chief Structural Design Engineer of Cargo Transport Complex Shared the Company’s Achievements
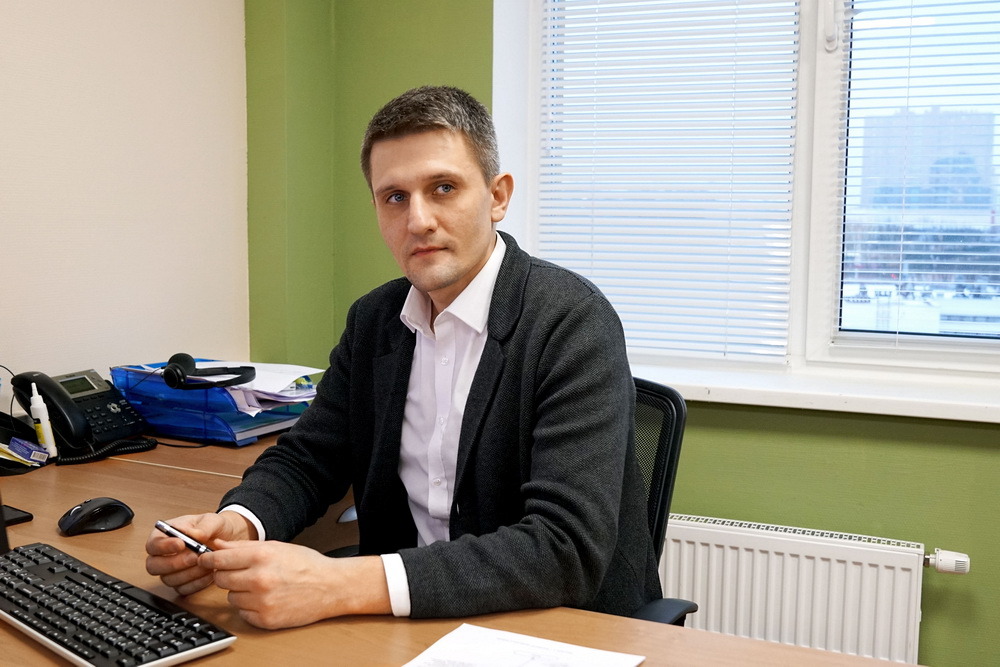
We continue the series of interviews on the performance of Unitsky String Technologies, Inc. Chief Structural Design Engineer of Cargo Transport Complex Dmitry Tikhonov told us about the work performed in the company this year in cargo direction.
Dmitry, what cargo vehicles are being developed and for which climatic regions?
Heavy-weight rail electric cars with load capacity up to 35 tons are developed in hinged and overhead modifications, including for transportation of ISO containers (note: ISO container is a standardized reusable shipping container intended for cargo transportation by different types of transport and used for mechanized transfer of cargo between vehicles).
It should be mentioned that we are developing such electric cars for arctic and tropical operating conditions.
Dmitry, could you describe your work with the cargo complex in the test center in Belarus?
In the EcoTechnoPark We continue to demonstrate and operate vehicles within the complex as well as perform scheduled monitoring of rail-string overpass structure through maintenance operations.
Meanwhile, our developers are designing an overhead unitruck with load capacity up to 15 tons.
Dmitry, what is uTrans complex? What is it designed to?
uTrans is a second-level string transport complex designed to deliver loose cargo by continuous bulk transportation without intermediate operational transshipments.
What are this year’s major outcomes in working on the complex that you can highlight?
During the year, we worked out and obtained the fundamental basis for a significant improvement of uTrans complexes in many directions:
Rail-string overpass. Application of modern materials enables to build a light-weight and strong structure with spans up to 1 km between intermediate supports. Importantly, such track structure can be adapted to any terrain and ensures competitive cost in terms of material intensity, as well as construction and assembly work.
Upgraded structure and operating principle of traction stations. Now they are combined into drive units, and the distance between adjacent units can reach 6 km.
By the way, the traction stations can now be serviced without stopping the whole complex while the modular principle ensures required backup power in all operating modes.
We also improved the cargo-carrying part of uTrans complex – continuous body belt. The developed solutions allow us to decrease peak-to-peak voltage variations on different parts of the route. This make the body belt more durable.
Continuous belt-type body of uTrans is loaded from a special terminal and unloaded die to inclined belt in the vertical plane. uTrans can operate continuously year-round and 24 hours a day.
The developed solutions to modernized structure of the bearing chassis allows replacement of bearing wheels while moving in automatic mode without stopping the whole complex, which immediately cuts operating costs.
Dmitry, are there any special features in the control system of uTrans complex?
Automatic control system of the complex operates based on the digital technology of uTrans. This technology ensure proactive feedback on compliance of operating conditions of the complex with all data obtained in real time. This makes it possible to operate uTrans complex in the most efficient modes.
The digital technology of uTrans allows scheduling “smart” routine maintenance based on real-time condition of the complex. Therefore, the complex can be repaired and upgraded the in short time and with minimum costs.
I’d like to mention that we’re focused mostly on achieving maximum automation and the capability to operate the complex continuously without pauses for routine maintenance and repair.
More news
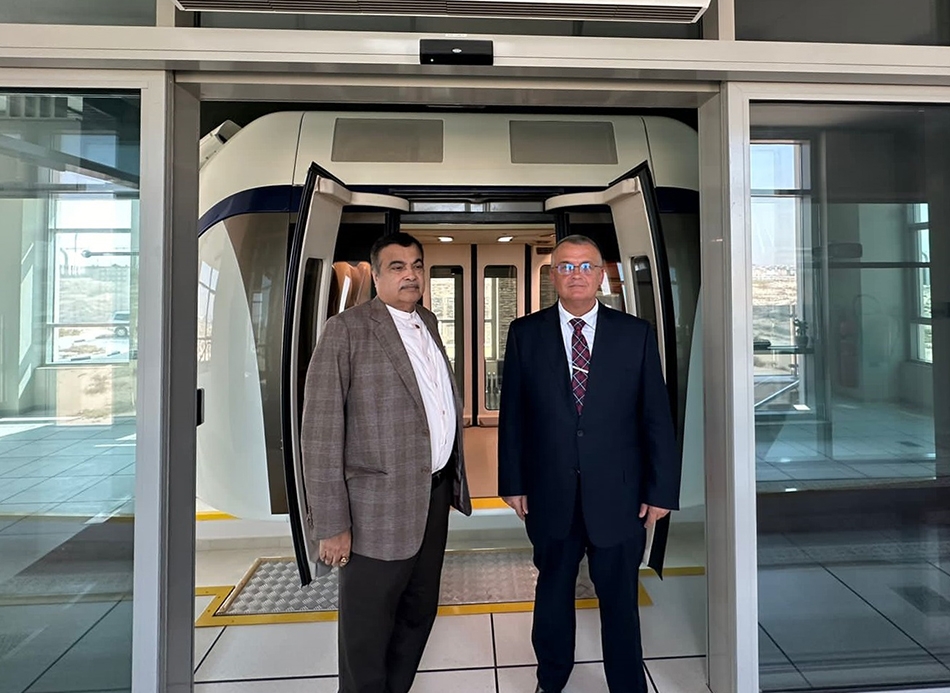
News
5 October 2023
uSky Visited by India's Minister of Road Transport and Highways
The high-ranking guest met with the Centre's management and evaluated the advantages of uST Transport & Infrastructure Complexes in action.
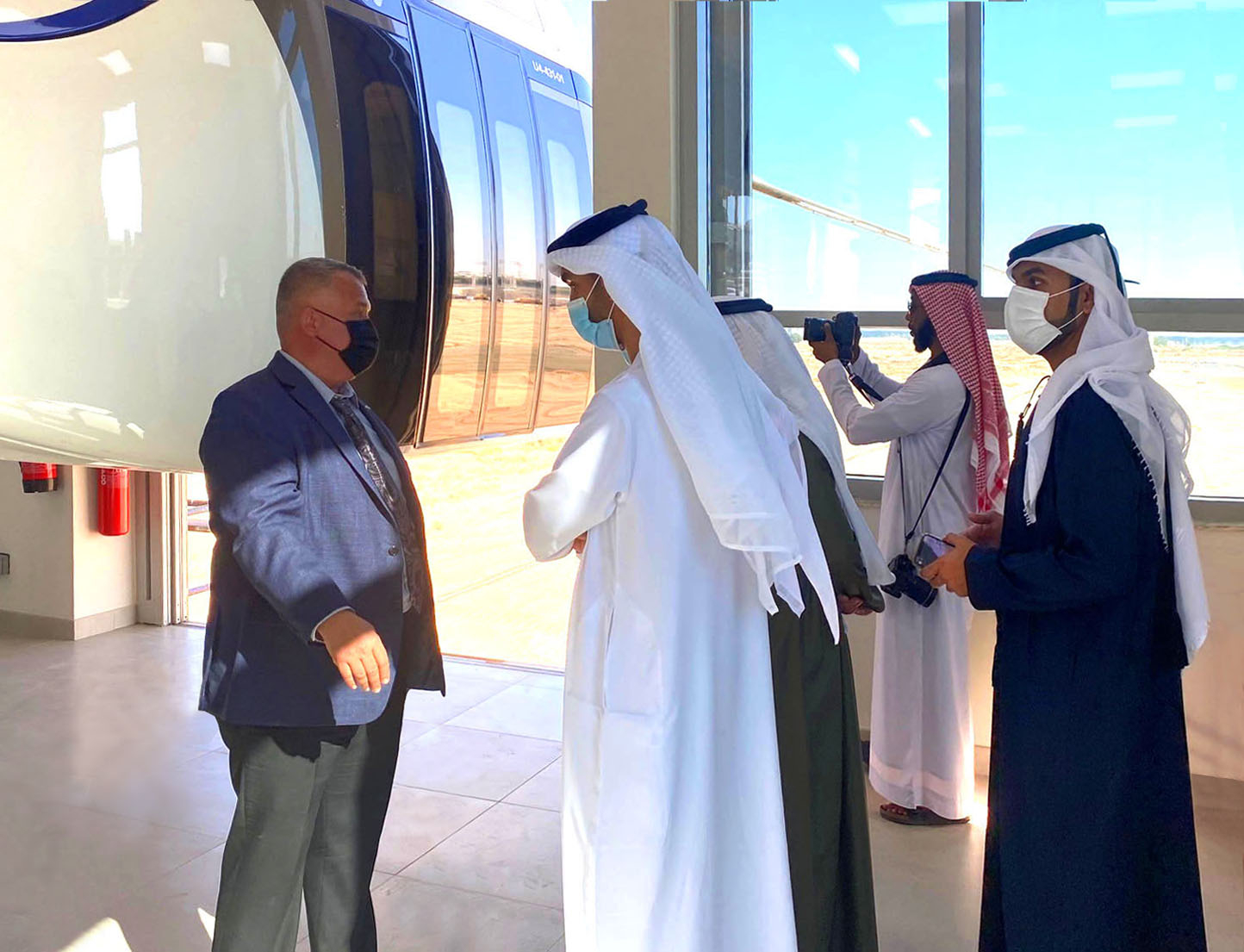
News
20 January 2021
UAE Government Ministers and Saudi Arabian Business Representatives Visited uSky Center in Sharjah
UST Inc.'s R&D Center at Sharjah Research Technology and Innovation Park (SRTIP) was visited by official delegations from the UAE government and Saudi Arabian businessmen announcing plans in 2021 to build an innovative transportation system “the Line” as part of NEOM Linear City Project.
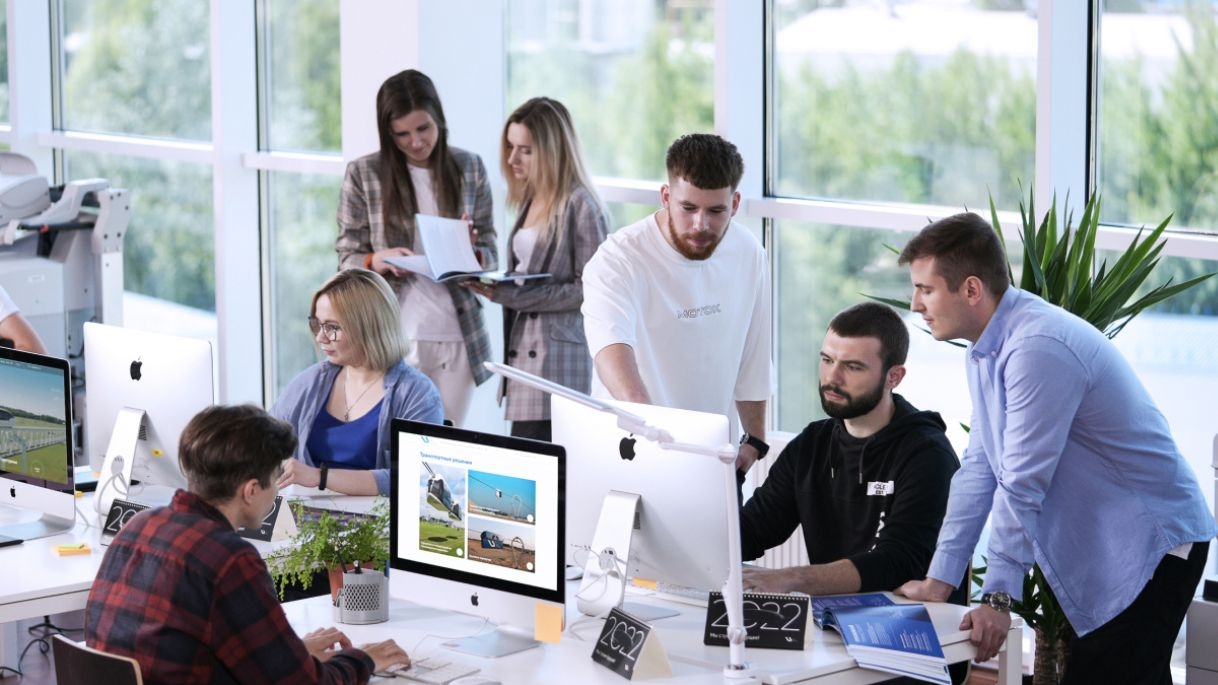
News
23 Junе 2023
UST Inc. Has Passed Another Audit of Its Financial Statements
Business Assurance LLC conducted an audit of the financial statements of Unitsky String Technologies Inc.